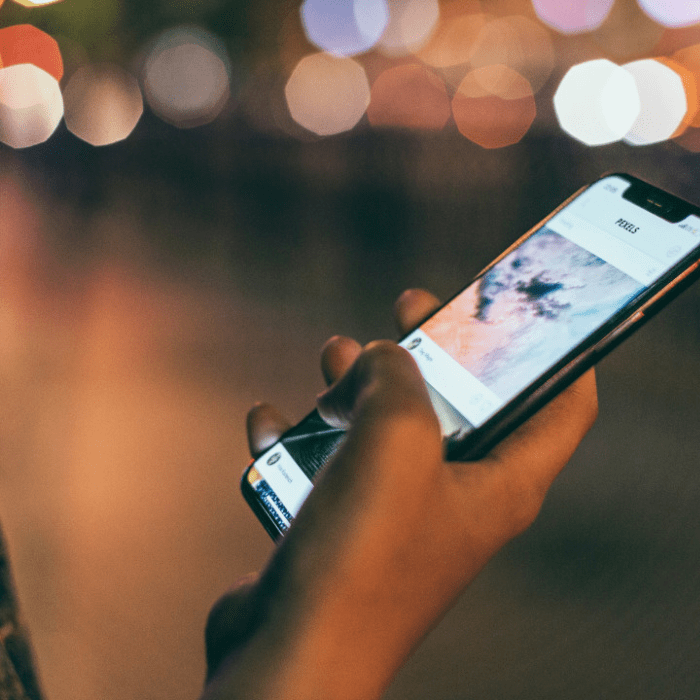
Scenario
AMcom's project for Cia Hering, Brazil's largest clothing franchise and one of the country's largest textile companies, optimized indicators by digitizing product development processes.
Business challenge
Cia Hering's quest for intelligent management of the various stages of collection creation and production led Brazil's largest clothing franchise to upgrade its industrial processes to Industry 4.0. With a PLM(Product Lifecycle Management) project developed by AMcom, the company reduced waste and production time, as well as gaining more assertiveness in cost analysis. This modernization improved the quality of the items manufactured and added transparency and value to the business.
Hering's main needs before implementing the new system were:
- Integration of people, data, processes and business systems;
- Optimization of product development in terms of cost and time;
- Managing the product life cycle with greater agility, quality and assertiveness;
- Guaranteed faster time to market.
In addition to providing these facilities, automation has brought greater agility to the development of knitwear products, improved communication between channels and supply and facilitated learning about the process.
Solution
To achieve Hering's goal of automating activities, AMcom brought together various design, production, digital manufacturing (DM) and collaborative management systems. In this way, every stage of product manufacturing - from creation to shop floor processes - is documented and available to the employees responsible, who can control the entire product and process life cycle.
Among the PLM solutions, AMcom has developed a simulation tool that optimizes the calculation of estimated production costs. Before the project was implemented, simulation was carried out manually using spreadsheets and calculators. Today, the tool automatically generates production costs by accessing the necessary information in the database. As a result, the collections can be altered, adapted, evaluated and, consequently, improved in the simulations carried out. Among the main changes brought about by this digitalization is a 20% reduction in costs for the production of Cia.
Results
The PLM project implemented by AMcom contributes to building a connected, integrated and responsive network of suppliers, guaranteeing production in audited factories, the quality of final products and a reduction in errors during the process.
Among the benefits of applying the project are:
- Facilitation of communication with the production area;
- Reduction in simultaneous engineering tests;
- Agility in monitoring samples;
- Measuring the volume of changes per period;
- Unified view of raw material stocks;
- Monitoring the size of the collection;
- Implementation of the cost analysis process;
- Assertiveness in the distribution of basic items;
- Monitoring sales/prices of campaign items.
Effectiveness
100% of production units audited.
25%
25% gain in on-time costs.
Strategic benefits
Assertiveness in costing new products and controlling production and stock.
Blog comments